The modern rubber pouring surface is actively used to create the most safe and comfortable, multi-functional playgrounds for games, walks, running, and various sports. This material is quite safe because the rubber pouring surface is a fairly reliable solution, it is a thick material that provides excellent adhesion to the sole of the shoe, making games as comfortable and injury-free as possible. A reliable rubber pouring surface is a high-class material that has a wide range of active applications. As mentioned above, this type of covering is considered the most optimal in the field of creating sports and children’s playgrounds for the following key reasons:
- There are practically no seams in this material, you only need to pour in place rubber surfacing. This favorably distinguishes the rubber bulk coating from other types of coating, in which the quality of the seams directly depends on the evenness of the base, the skill of the installers, and the glue used;
- Other types of coating have the risk of cracks and deformation of seams during winter and spring temperature changes and thawing and freezing cycles, which cannot be said about the modern rubber pouring surface;
- Rubber bulk coating can be laid on an uneven surface with almost any relief – this reliably allows you to implement all kinds of safe slides on children’s playgrounds. But you need to understand that if you need a flat surface – miracles do not happen, the poured rubber coating will completely repeat the terrain on which the site is located.
What is Pour in Place Rubber Surfacing?
The rubber pouring surface is a modern, reliable completely safe, durable material consisting of rubber crumb obtained during the processing of car tires and polyurethane, which is the latest achievement of the chemical industry. This type of surface is extremely popular nowadays because the materials from which the rubber pouring surface is made are durable and do not lose their properties under conditions of constant use. Each component present in this coating gives it its key, unique properties. Rubber, which is the dominant component in the structure of this coating, makes the surface extremely flexible and durable, resistant to various weather conditions and temperature changes. The rubber pouring surface withstands enormous loads and shocks in a variety of conditions, the surface does not deform under such conditions of use. The rubber pouring surface does not crack during active operation, does not tear, and has high elastic properties. Polyurethane binds the composition and gives the coating very high adhesion, due to which the rubber pouring surface lies on almost any hard surface – concrete, asphalt, metal, and wood. It is extremely difficult to separate the rubber pouring surface.
Limitations of Rubber Surfacing
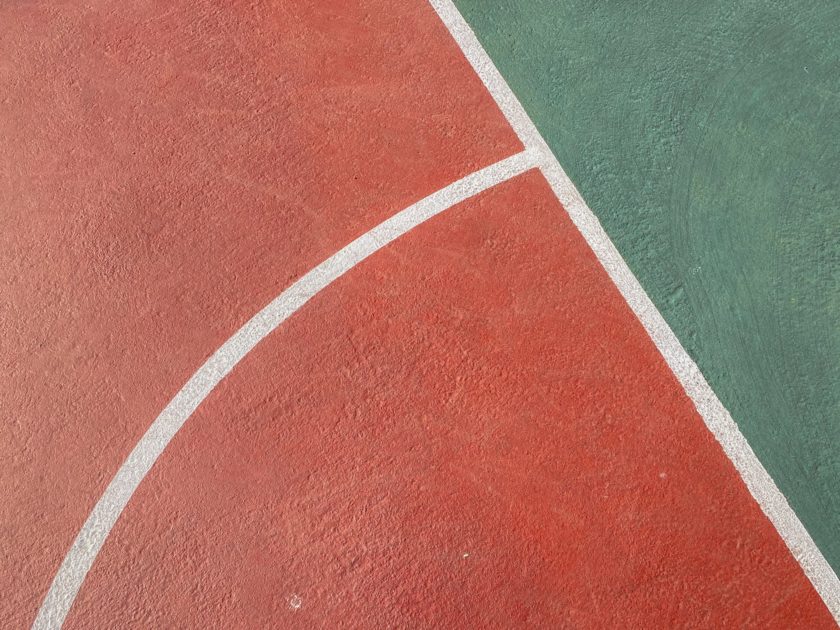
If you’re looking to build a sports or playground, investing in infill rubber is the right decision for several key reasons, including:
- Incredible durability – there is practically no risk of cracking;
- Easy maintenance;
- Maximum safety on children’s playgrounds, the uncompromising flat surface avoids the danger of tripping and falling;
- The rubber pouring surface is an ideal solution for people with physical disabilities/restrictions;
- Rubber Resurfacing Repair does not emit harmful chemicals and does not use materials such as wood or metal that can cause skin irritation and other health problems;
- The visual aesthetic is much more colorful, bright, and cheerful compared to traditional playground materials.
The standard version of the rubber bulk coating is 10 mm thick. This is a completely working and widely used option, for example, as a rubber covering of sports fields. Colors can be different, there are no restrictions.
Solutions and Best Practices
The key solutions provided by rubber infill surfaces are excellent because this non-slip, safe, wear-resistant surface is actively used in the creation of sports and children’s playgrounds, tennis courts, and swimming pool surfaces. The rubber bulk surfaces are completely hygienic, they provide a wide range of impact-resistant support, high water resistance, and strong protection against slipping. How is the process of installing rubber pouring surfaces successfully implemented? A truck with a concrete mixer arrives at the place of creation of the site, which is created based on a rubber pouring surface, where rubber crumb, polyurethane, and dye are mixed in strictly defined proportions. Then this mixture is applied to a previously carefully prepared (leveled) surface and the mixture is applied evenly over the entire surface (so that the thickness is the same everywhere) with special construction tools. In practical terms, experience and professionalism are required for a successful installation process of a rubber pouring surface, because many key, critical nuances need to be taken into account, in particular:
Polyurethane filler is the most expensive component of the rubber pouring surface, it comes from different manufacturers and, accordingly, has a different quality. The use of a polyurethane filler that has not been tested in practical operating conditions is associated with a high risk that next year you will face the problem of damage to the coating as a result of changes in the external temperature. It is necessary to strictly observe all the requirements regarding the installation process of the rubber pouring surface. Sometimes some unscrupulous suppliers do not comply with these requirements, as a result of which the coating in a short period begins to receive certain damages, so it is important to entrust the installation process to professionals with the appropriate level of practical experience.
The base for pouring the rubber coating must be solid – asphalt or concrete. It is desirable to have a minimum slope so that water does not stagnate.
Weather conditions in the process of installing rubber bulk coating, this is also a critically key aspect that is important to consider and adhere to. High-quality installation of rubber bulk coating is successful only if all installation work is carried out in dry weather and at an air temperature of more than 10 degrees.
Conclusion
Summarizing all of the above, we can say: that due to the numerous positive properties of rubber bulk coating, the scope of its use is a very effective process. To obtain a high-quality coating, binders are added to the composition, which give the material elasticity, and also ensure strong adhesion to the base. When using this coating, the surface is reliable, flexible, and very durable. The process of obtaining the desired colors for rubber bulk coating is carried out by adding various dyes. Rubber bulk coating can be used both indoors and outdoors, at any time of the year, and in any weather. The key advantages of using a rubber bulk coating include the following points:
High wear resistance and durability. The level of safety with proper installation and timely maintenance is very high.
Good cushioning effect. This is a completely impact-resistant coating.
Simple and quick installation process. Such a coating is even and fills small defects of the base.
Aesthetics. Thanks to the wide range of colors and the variety of possible combinations, the rubber pouring surface looks as attractive as possible. Such a coating is quite resistant to sunlight and insensitive to aggressive environments such as acids and solvents.
Absolute safety. This material is non-toxic, and does not emit substances harmful to health, so the rubber bulk coating can be used on children’s playgrounds.
It has excellent anti-slip and impact-resistant properties.
Maintenance of the coating is simple.
If the damaged area of the coating needs to be replaced, it is possible to partially repair the coating, saving considerable money.
So that the rubber bulk coating can be used for a long period and enjoy high quality, it is important to carefully follow the technique of its application. You should entrust the installation process to professionals.